The little gizmo that is supposed to hold the accelerator cable in place is a small piece of black plastic that does not hold it securely. As I want to be sure nothing falls apart (like my current cable), I made another end. Here are the pieces:
The black object is the holder that came with the kit. The brass object is a 1/4" brass pipe coupler with one end cut off. The steel "deally" is the holder. The large end is threaded 1/4" tapered pipe and the cable sheath slides into it, the other end is 5/16"-24.
Here it is assembled. The tapered pipe thread clamps the "deally" onto the cable sheath pretty tightly. Sure is not going to fall out.
Onward to the accelerator cable bellcrank. Started with a piece of .100" galvanized stock I had laying around. There is nothing magic about the size of the piece, it was a handy sized scrap that I have hoarding for 20 years.
You can see the line that I scribed in order to get some sort of alignment. The tool being held in the vise is a neat little piece of Chinese rubber dog poo. It is held in the vise with strong magnets. Eat your heart out, Rick.
The finished bend. Automatically gives a 90* bend, will bend anything that you and your vise are capable of.
The blade is not hard, so round stock produces a nice cresent shaped ding. Don't ask.
Bill
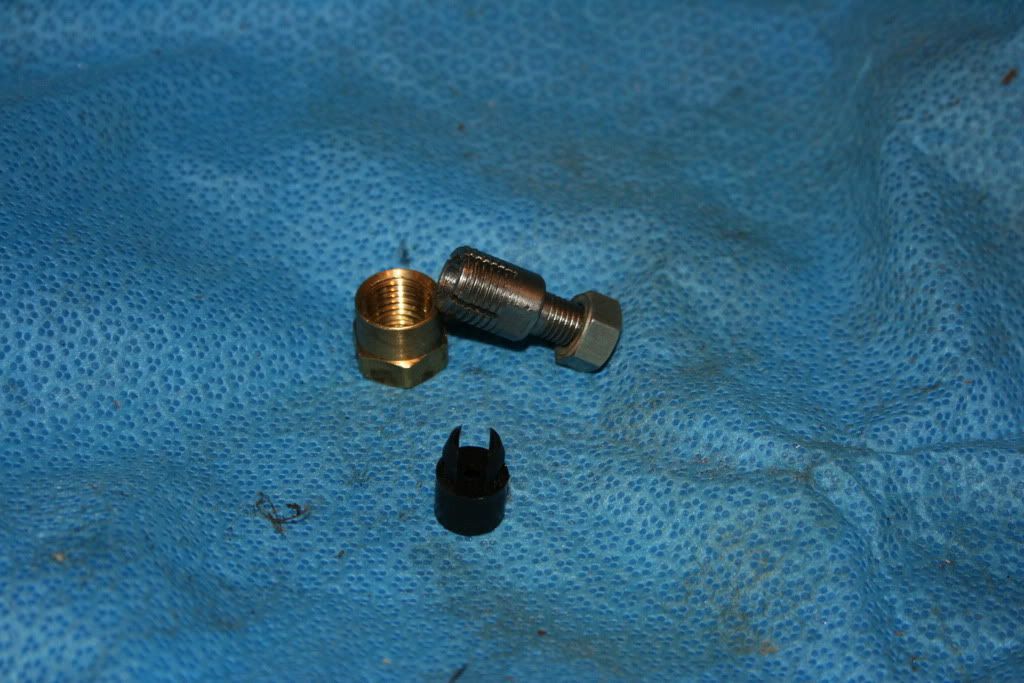
The black object is the holder that came with the kit. The brass object is a 1/4" brass pipe coupler with one end cut off. The steel "deally" is the holder. The large end is threaded 1/4" tapered pipe and the cable sheath slides into it, the other end is 5/16"-24.
Here it is assembled. The tapered pipe thread clamps the "deally" onto the cable sheath pretty tightly. Sure is not going to fall out.
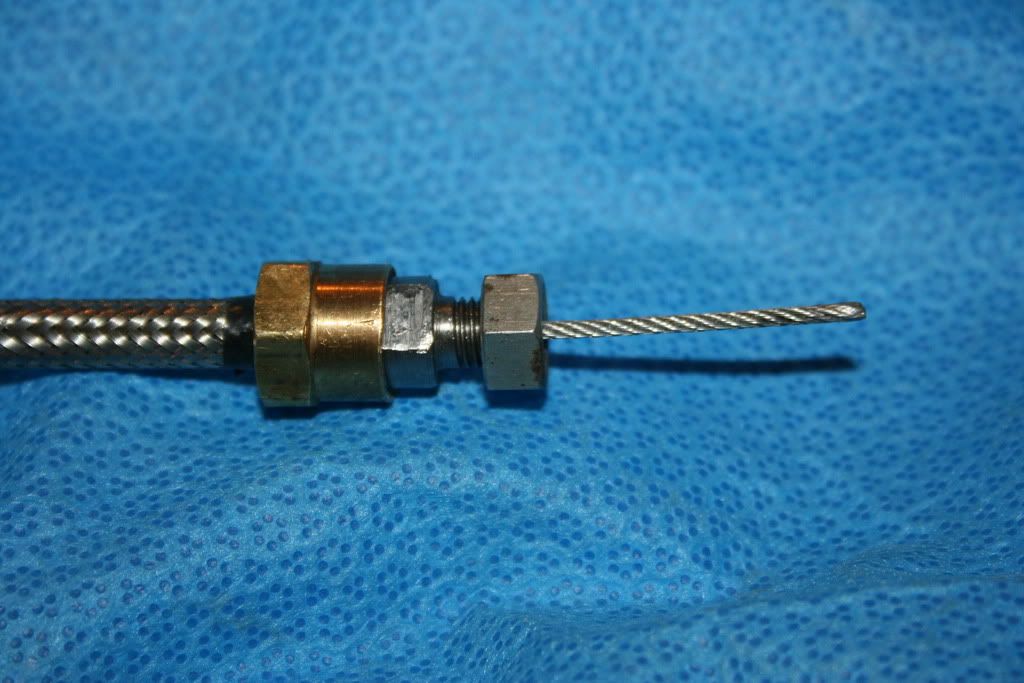
Onward to the accelerator cable bellcrank. Started with a piece of .100" galvanized stock I had laying around. There is nothing magic about the size of the piece, it was a handy sized scrap that I have hoarding for 20 years.
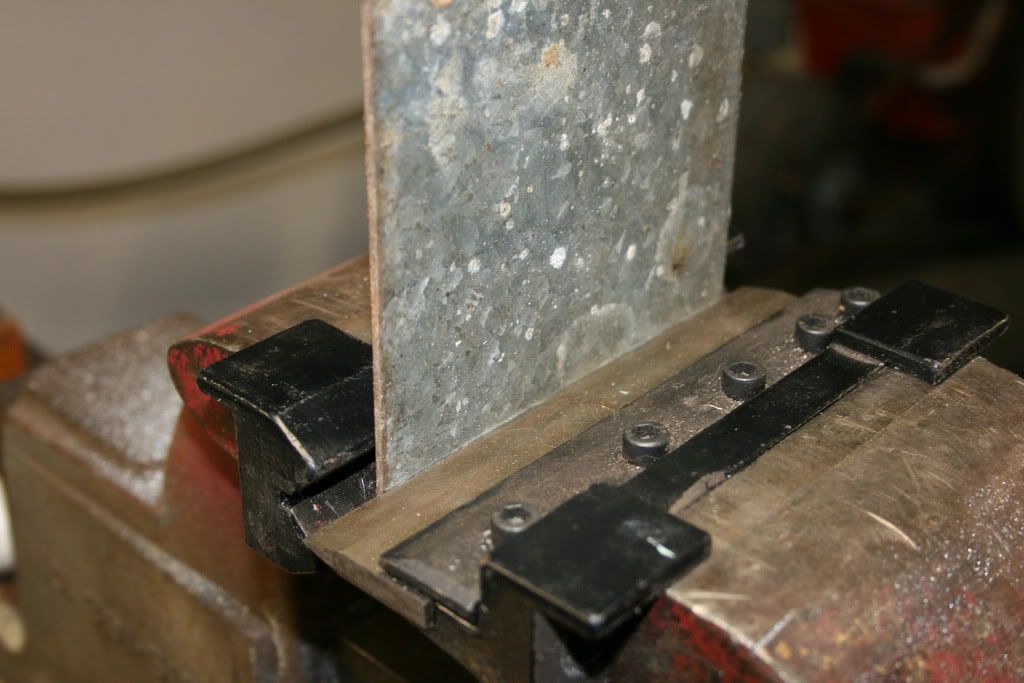
You can see the line that I scribed in order to get some sort of alignment. The tool being held in the vise is a neat little piece of Chinese rubber dog poo. It is held in the vise with strong magnets. Eat your heart out, Rick.
The finished bend. Automatically gives a 90* bend, will bend anything that you and your vise are capable of.
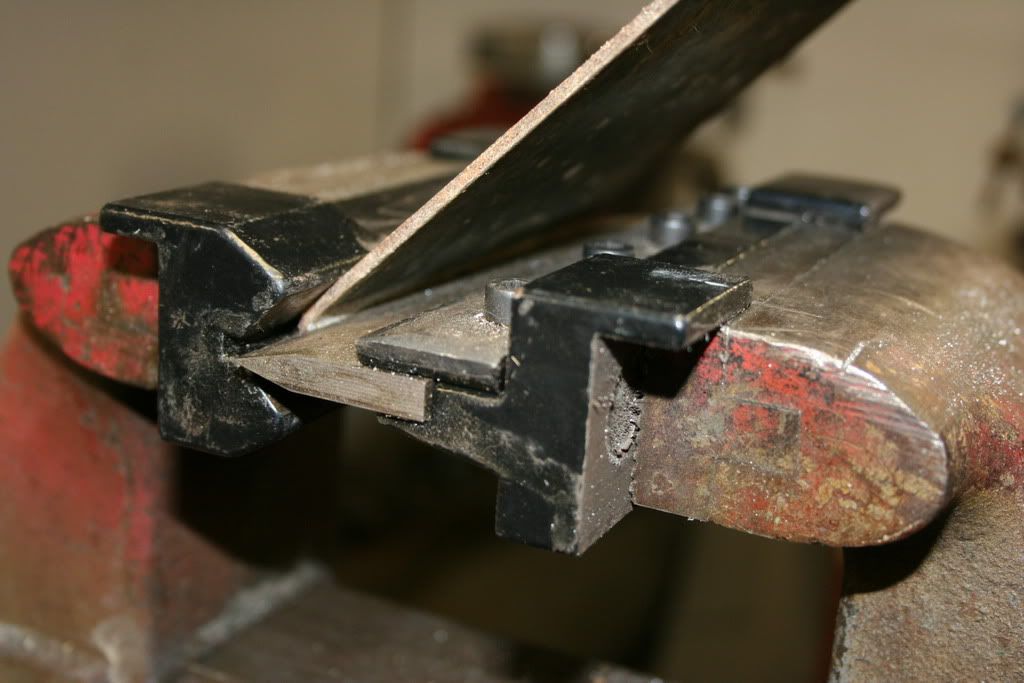
The blade is not hard, so round stock produces a nice cresent shaped ding. Don't ask.
Bill